Aug 11, 2020
Stress – Even Boat Lifts experience it
Stress – Even boat lifts are under stress – this year more than ever before due to the high waters.
Why? High water increases the stress on your cables.
We’ve previously informed you of the danger to boat lift cables during a storm. If the waves hit the bottom of your boat it will momentarily lift the boat and then allow it to fall back on the rack. What if the cables are weakened by rust and frays? The “bouncing” effect can completely sever a cable into two pieces.
The boat only lifts a fraction of an inch – right?!!
How can that movement harm the cables?
Even though the boat only rises a fraction of an inch, the energy of the “falling” boat must be absorbed by the boat rack. The cables in each corner of the lift must, in turn, absorb the stress of a moving 3-5,000 pound boat.
Having said that, a weakened cable is in imminent danger of breaking. Think of an 80-100 lb jackhammer used to break up concrete. Even reinforced concrete can not withstand the movement of the bit hitting the concrete.
With a boat, you are talking about a potential 5,000 lb weight dropping on a rack compared to an 80-100 lb. weight.
Protect your cables! It only takes a minute or two to protect your cables from rust. It’s simple and easy to do. A convenient link* is provided below so you can learn more about this.
What are the defect warning signs?
There are warning signs of defects in your cables? If your cables look like any of these, it’s time to replace them. Need more information? Here’s an article that addresses this issue.
Always remember – it is possible to have broken strands inside your cable without any exterior signs of damage. This situation is especially true on stainless steel cables which do not rust.
What’s a quick way to reduce the stress on the cables?
At the beginning of the year, we place your boat lift in the requested location. We adjust the height of the legs based on what the current water level is.
Unfortunately, the water has continued to rise this year and that may no longer be suitable for the conditions you have today. Add to this the Seiche waves (pronounced “say-sh”) which are standing waves that form in a confined body of water. The friction of the wind against the surface of the water causes wave action.
As waves move towards the shoreline the water gets shallower and the moving waves rise higher. Standing waves, in general, can form in any type of semi-enclosed or enclosed body of water. When these rising waves hit the bottom of your boat the boat does what it is designed to do – it floats on the water.
Your Lift rack may be too close
The lift rack could be too close to the water to protect your boat with the rising water. As a result, you are not able to raise the boat high enough to keep it above the waves. On the other hand, If the rack is set too high in the water, you may not be able to get your boat on the lift. It’s a delicate balance. The variable is the changing depth of the water.
What can I do?
One way to raise the boat higher is to purchase longer legs and replace the standard lengths with new ones.
A less costly alternative is to simply move your lift closer to shore. It will be in shallower water and save you having to buy longer legs and the labor to install them.
If you keep the standard legs and don’t allow us to place the lift closer to the shore, you are inviting costly repairs or even replacements.
In Conclusion
Get out there and take care of those cables. Check out the link below. Then, consider moving the lift closer to shore.
* Wire Rope Lubrication link.
Tell Your Friends & Family
Have friends or neighbors you believe should see this article? Email them a link to this article – and Thank you!
You can visit Pier & Waterfront Solutions on Facebook also.
Don’t Forget – PWS is the expert when you have a waterfront problem!
Where is Pier & Waterfront Solutions?
Located at 7325 St. Hwy 57, we are about 3 miles south of Sturgeon Bay, and 1 mile past the intersection of Cty MM (heading north). Look for the intersection of Idlewild Road and Hwy 57.
ARE WE OPEN?
Pier & Waterfront Solutions has remained “open.” We have implemented measures to ensure the safety of our employees and visitors. As of Aug 1st, Wisconsin mandates the use of face masks. We also endorse this to slow the spread of Covid-19. It’s the only known method to control the spread at this time.
While all this is going on, we are working to maintain the trusted service you expect. That’s important to us.
We are conducting as much business as possible by email, text, or phone. Site visits will continue as usual. When in-person contacts are necessary, we follow “social distancing” guidelines as closely as possible.
When can I see the display yard?
Our display yard is always open for you to examine at your leisure. All displays have a numbered, red tag on them. If you want more information or pricing, please reference that number.
How will I get my estimate?
We provide estimates and invoices by email to make the process paperless and faster. With these measures, we hope everyone will stay safe, and we will be back to normal operations soon.
What can YOU do to help our crews?
Please conduct as much business as possible via emails, messaging, and emails. When you see our crews working in your area, please practice “social distancing.”
Call, message, or use this simple request form to get answers and quotes.
Thank you for allowing us to work with you – safely.
Let’s all stay safe!
Jun 16, 2020
A Boat Lift Safety Lesson
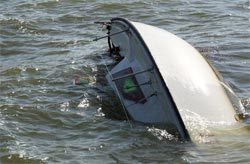
My lift cable broke…and I can’t ….
Proper boat lift safety means you won’t have to learn the tough lesson pictured here. If you apply these recommendations, you can relax and enjoy your boating experience.
Failure to follow these safety suggestions may result in damage to your boat or even personal injury.
Boat Lift Safety = Never exceeding the Ratings
The rated capacity of any lift is the maximum capacity, and you should never exceed that amount.
Boat weight INCLUDES more than just the published weight of the boat. It also includes the weight of fuel, water, and equipment. After all, you will be lifting all of this when you raise your boat. It adds up very quickly!
Plus, we recommend that you allow at least a 300-500# margin of error when you calculate the boat weight. See also: Sizing a Boatlifts: How to select the correct Boat Lift.
If you ever hear a salesperson say, “You can easily go 40% or 50% over that rating without a problem”. You are at risk of being the owner of the boat above if you follow that flawed thinking.
What’s the real story?
Lift cables are rated much higher than the rating of the boat lift. As an example, (using imaginary numbers) your boat lift has a 4,000# rating, it could have cables rated for 6,000# to 8,000#.
The cable rating may be 6,000#, but ONLY if the wires are in perfect shape – meaning no burrs, kinks, frays, or rust. These defects reduce the load capacity of the cables.
The lift racks are correctly rated for the weight regardless of the cable ratings. If someone is trying to sell you a 4,000# lift and telling you that it can handle up to 4,700# – WALK AWAY!!
The load must also be “balanced” on the rack for proper boat lift safety. (More on this later)
Lift cables fail without warning
Sorry!! Cables don’t “creak” or “groan” as a warning of impending danger. The only sound you hear is a loud “snap” followed by the sound of your boat hitting the water.
In a storm, you want to get your boat as high above the water as possible. Yet, raising a boat until the lifting platform or rack hits the frame is NOT the way to do it.
Hitting the frame is an all too common occurrence. Ask yourself, if raising the boat that extra ½” is worth snapping a cable. You risk damage to your boat and lift, or worse yet, personal injury.
Operate Lift Motors properly or break a cable
Properly used, an electric lift motor is a real back saver! I wouldn’t be without one. But you need to exercise extra care when using a lift motor. Shutting off a lift motor does not mean the lifting action will stop. What if it “drifts”?
For example, one brand of lift motor “drifts” after the motor stops. The “drift” potentially causes the lift rack and frame to jam together.
Cable failure, lift or boat damage, personal injury, or worse may be the result.
When the rack hits the lift frame, something has to give. The most likely culprit will be the cables. If you combine a damaged cable with a rack hitting the frame, you have a recipe for disaster.
OK, You Jammed the Rack & Frame! – What comes next?
You were distracted, and now the rack is jammed against the frame. A jammed rack means your next step is critical.
You’re in a hurry to release the pressure, but be sure you know which way the motor will go when you flip the switch.
If the rack isn’t going “DOWN,” damage occurs almost instantly. If it is a broken cable – your boat goes down – even faster!! Starting the winch or motor in the wrong direction could mean your boat will be in the water in an instant. Did I mention it won’t be floating?
Proper Positioning of the boat is part of boat lift safety.
As if a jammed rack wasn’t enough, did you know there are right ways and wrong ways to position your boat on your lift?
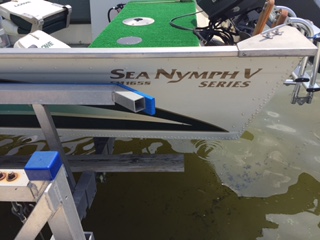
Boat stern overhanging too far
All lift ratings are based on a “balanced load.” In other words, the weight of the boat must be relatively equal on each end of the rack.
When you put the majority of the weight on one end of the rack, cable breakage is more likely.
The heaviest part of any boat will be where the engine is mounted. That could be at the stern (outboards) or even near the middle of the boat (inboards).
A boat placed too far forward on the lift rack results in excessive weight on the “front” of the lift. Too far to the stern of the boat puts too much weight on the rear cables. If the cables have weakened by corrosion or fraying, you risk impending disaster.
What is the correct position for a boat on a lift?
You can determine the proper positioning of a boat by placing the stern of the boat within 12″ – 18″ of the rear lift rack. Now, raise the rack slightly out of the water.
Next, try to lift the bow end with your hands. If the boat weighs 3,500# and you can lift the front of the boat, you are either “Mr. Atlas” or the boat is positioned to the rear. If you can lift the bow at all, your boat is too far back. The weight is not evenly distributed across the four corners of the lift. Lower the boat and reposition it forward.
The boat shown here overhangs about 36″ from the rack and risking major damage. By placing the boat too far back on the rack, a majority of the weight is on the rear cables. What if those cables are weak from corrosion or fraying?
Does high water affect the positioning of a boat?
Yes, it does. In the example above, with the rear of the rack overloaded, the boat has only minimal weight on the front rack.
Your boat will float on a wave. When the bottom of the boat is “lapped” by a wave, it will try to raise the boat. With repeated lifting (or bouncing) the boat can work it’s way off the rack. It will try to go go to the rear. Eventually, the boat will literally “bounce” right off the lift.
With a balanced boat, you have a better chance of the boat staying on the rack.
Align the boat in the same position each time.
So, now you have repositioned your boat until you found a good position for a balanced load. What comes next?
It’s time to make a note of a fixed object on the boat and how it lines up with something on the lift. This is a good gauge for the next time you enter your lift. Always try to go back to this same position.
Summary
You now know the do’s and don’t of boat lift ratings and positioning for your boat. With this knowledge, you can Relax and Enjoy your boating experience.
Where is Pier & Waterfront Solutions?
Located at 7325 St. Hwy 57, it’s 3 miles south of Sturgeon Bay, and 1 mile past the intersection of Cty MM (heading north). Look on the right side, one mile north, at the next intersection (Idlewild Road and Hwy 57).
ARE WE OPEN?
During this time of uncertainty, Pier & Waterfront Solutions is staying “open.” We have implemented measures to ensure the safety of our employees and visitors. At the same time, we are working to maintain the trusted service that you have come to expect.
We are implementing these precautionary measures:
1. Conducting as much business as possible by email, text, or phone.
2. Site visits will continue but with limited in-person meetings. When in-person contacts are necessary, we will follow “social distancing” guidelines.
3. Our display yard is always open for you to examine at your leisure. All displays have a numbered, red tag on them. If you want more information or pricing, please reference that number.
That’s not all!
4. Some employees are working remotely, but they are always available by phone.
5. Any employee exhibiting symptoms or illness is sent home.
6. We provide estimates and invoices by email to make the process paperless and faster.
7. Crew starting times are being staggered to limit social interactions.
8. We keep the same crews together to limit cross interactions.
With these measures, we hope everyone will stay safe, and we will be back to normal operations soon.
What can YOU do to help us?
1. Please conduct as much business as possible via emails, messaging, and emails. This step protects everyone involved.
2. When you see our crews installing equipment, please practice “social distancing.”
So, YES – WE ARE OPEN!
Please call, message, or email us with any questions.
Thank you for allowing us to work with you.
Let’s all stay safe!
Contact:
Jerry @ (920) 493-4404 or Jerry@wisconsinpws.com – Commercial work & new/used Sales.
Dave @ (920) 905-2588 or Dave@wisconsinpws.com – Erosion control & shoreline work.
Jerry @ (920) 493-4404 or Jerry@wisconsinpws.com – Scheduling & Service work
Jun 9, 2020
32 STEP CHECKLIST FOR A BOAT
This 32 step checklist for your boat will start your boating season off right.
Do you have spring fever? Are you itching to get your boat or jet skis back in the water? It’s been a L-O-N-G winter. Now it’s time to de-winterize your boat before taking it out for its first trip of the season.
Following a spring checklist, like the one below, can help prevent a host of problems. Skipping them could keep you out of the water later in the season.
We all know how fast storms come up on Green Bay. Don’t get caught unprepared. Make sure the boating season goes smoothly and safely.
HERE’S A SPRING CHECKLIST FOR A BOAT:
- Is your boat registered?
- Be sure to empty the old fuel and add fresh fuel.
- Are the fuel shut-off valves on the tank and at the engine working?
- Is your blower switch (if any)working?
- Recharge your battery and fill with distilled water, if needed.
- Secure the batteries in ventilated containers that are non-corrosive and liquid-tight.
- Fit non-conductive covers over the posts.
- Is the lower-case leak-free?
- Check the electrical system, including fuses, spark plugs, and wires.
- Inspect the propeller for damage.
- Is there any damage to the hull (blisters and cracks)?
- Flush the water tank.
- Replace any oil filters and lubricate all parts.
- Are all lines checked?
- Check the hydraulic steering system for leaks and fluid levels.
- Inspect the steering and throttle cables.
- Are all fire extinguishers charged?
- Is everyone familiar with how to operate them? Make sure that at least one can be reached from the helm or cockpit.
- Are life vests checked for wear, abrasions, weak or torn seams, secure straps, and buckles?
- Inspect the bilge pump, if any, for cleanliness and absence of obstructions. Check this frequently throughout the season.
- Check the engine compartment for excess water.
- Are the lights on your boat operational?
- Check the electrical cables and connections for loose, disconnected, or corroded conductors.
- Have you taken a boating safety course?
NOW YOU’RE READY TO GO.
- If you are towing your trailer to its launch point, you will also need to inspect it before your first outing. In particular, are the lights working properly?
- Be sure to tell someone responsible where you’re going.
READY TO LAUNCH
- Is the drain plug in place? You’d be amazed how often this happens.
- Follow all safe launching practices.
- Watch for kids in your path.
- Ventilate the bilge for several minutes before starting the engine.
- Watch the engine temperature and cooling system.
- Make sure everyone follows safe boating practices.
Now you’ve done the work – It’s time to enjoy the benefits!
Tell Your Friends & Family
Have friends or neighbors you believe should see this article? Email them this link – and Thank you!
Don’t Forget – Considering rip-rap for your shoreline? PWS is the place to contact!
Where is Pier & Waterfront Solutions?
Located at 7325 St. Hwy 57, it’s 3 miles south of Sturgeon Bay, and 1 mile past the intersection of Cty MM (heading north). Look on the right side, one mile north, at the next intersection (Idlewild Road and Hwy 57).
ARE WE OPEN?
During this time of uncertainty, Pier & Waterfront Solutions is staying “open.” We have implemented measures to ensure the safety of our employees and visitors. At the same time, we are working to maintain the trusted service that you have come to expect.
We are implementing these precautionary measures:
- Conducting as much business as possible by email, text, or phone.
- Site visits will continue but with limited in-person meetings.
- When in-person contacts are necessary, we will follow “social distancing” guidelines.
- Our display yard is always open for you to examine at your leisure. All displays have a numbered, red tag on them. If you want more information or pricing, please reference that number.
Is there More?
- Some employees will be working remotely, but they are always available by phone.
- Any employee with symptoms or illness is sent home.
- We continue to provide estimates and invoices by email to make the process paperless.
- Crew starting times are being staggered to limit social interactions.
- We keep the same crews together to limit cross interactions.
With these measures, we hope everyone will stay safe, and we will be back to normal operations soon.
What can YOU do to help us?
- Please conduct as much business as possible via emails, messaging, and emails. This step protects everyone involved.
- When you see our crews installing equipment, please practice “social distancing.”
Thank you for allowing us to work with you.
So – YES – WE ARE OPEN!
Please call, message, or email us with any questions.
Let’s all stay safe!
Contact:
Jerry @ (920) 493-4404 or Jerry@wisconsinpws.com – Commercial work & new/used Sales.
Dave @ (920) 905-2588 or Dave@wisconsinpws.com – Erosion control & shoreline work.
Jerry @ (920) 493-4404 or Jerry@wisconsinpws.com – Scheduling & Service work
May 14, 2020
USED BOAT LIFT GUIDE – Part 2
Are you thinking about buying a used boat lift? This two-part series concludes with four additional items to check. Upon completion, we will have guided you through eight problems to look for when buying a used boat lift.
See Part 1 for the first four checks.
Here’s the second list of things to check:
- Does the cable wind smoothly and correctly on the winch?
- Do the cables have rust on them? Does it use galvanized or stainless steel cables?
- Are there any “kinks” or other visible problems on the cable?
- How often were they lubricated, and with what lubricant?
Does the cable wind smoothly around the winch?
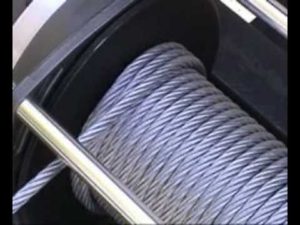
Properly wound Boat lift cable
If you look up inside the winch housing, if it has an enclosure, you will be able to see how the cables are winding. It should be a smooth pattern without any “crossed” cables. If the winch has no outer covering, you can readily see the pattern.
The wire cable has a “memory” to it. Once the cable gets crossed, it will tend to do it again the next time the cable rewinds.
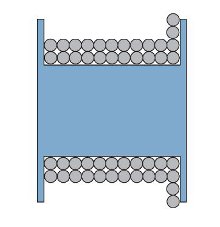
Typical Cable Stacking
If the cable is wrapping in layers, you will get a thunderous sound when the cable finally “falls off” the stack. This movement scrapes the galvanizing of the wire, and rust will form. The “shock” of dropping a 2,000# (or more) weight will also apply excessive stress on the cables.
Do the cables have rust on them?
Galvanized cables will rust over time. The movement of individual strands of the wire against each other cause rust. This movement occurs as they wrap around the winch and pulleys. There is no way to end this.
The only thing you can do is lubricate the cables. The lubrication reduces the friction between individual strands. Lubrication, in turn, lengthens the life of the cable. For more details click HERE.
Rust on the cable indicates that some galvanizing has worn off. Individual wire strands are compromised.
What about rust on a stainless steel cable?
Stainless steel does not rust, but it does pick up loose rust from the winch. Winches are plain steel with a painted surface. When the paint rubs off, the steel will rust and “bleed” onto the cable.
It’s much like a scratch on a car. The rust will run down the side of the vehicle.
The rust typically appears near the winch when the rack is in a lowered position. Under these circumstances, it’s ok. Try to lubricate the cables every year to slow this down.
Are there any visible signs of problems with the cables?
We recommend you lower the “rack” down, but DO NOT allow “slack” to form in the cables. Slack in the cables will allow the windings at the winch to unwind and cross over each other.
It’s much like a fishing reel getting snagged when there is no tension on the line.
Are the cables on the used boat lift adjusted equally?
If three of the four corner cables appear “tight,” the cables will need re-adjustment to re-distribute the weight equally.
Even proper positioning of the boat is essential.
If it takes excessive weight to lower the rack, look at the pulleys in each corner. Are they free to move? Is there sand, seaweed, or reeds packed around the pulleys? Remove any debris to free up the rack.
If any pulleys resist rotation, the rack will not lower smoothly. You must find out why the rack is not moving.
Note: In the case of jet ski lifts, the weight of the rack may not be enough to cause the rack to lower by itself. Have someone lean of the back of the lift to assist the rack in lowering. Still, hanging up? Check all the pulleys as above.
Check the fittings on the ends of the cable. Has rust formed on the fittings, or are there broken strands?
Caution– watch out for the ends of the cables. It’s a painful reminder of exposed strands.
Examine the entire length of the cable for frays (broken strands).
Caution – DO NOT run your hand up and down the cable without leather gloves. Broken strands on the cable will cause painful cuts on an unprotected hand. Ordinary cloth gloves will not protect your hand.
Are there any “kinks” or other visible problems?
Here are the warning signs of defects in your cables.
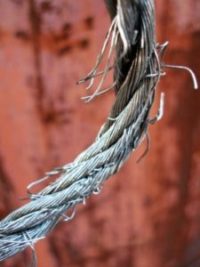
Frayed Boat Lift Cable
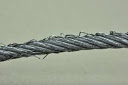
Broken cable strands
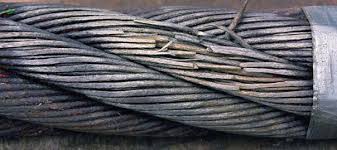
Cable damage
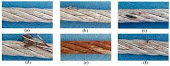
wire rope damage
If your cable looks like any of these, it’s time to replace them.
Warning – it is possible to have broken strands inside a cable without any exterior signs of damage. This situation is especially true on stainless steel cables which do not rust.
Read this article to learn how to lubricate cables. Lubrication slows down premature corrosion. It’s simple and easy to do.
What is the proper lift cable maintenance?
Cable replacement requires a visual inspection of the lift cables. It’s best to inspect it while it is on dry land to check the critical points. Ideally, the lifting platform (or rack) should be in the lowered position. Of course, make sure the lift cable is not allowed to go slack.
Examine the vertical length of the cable for frayed wires, especially near the winch. Excessive fraying or corrosion near the winch is a top signal of damage.
CAUTION – Always wear leather gloves when sliding your hands along the cable. A frayed wire can cause painful damage to unprotected hands.
There are two types of cable wear:
- Internal cable abrasion- Occurs whenever strands work against each other under load.
- External abrasion – Occurs when the cable bends around the winch drum or against the side of the drum.
Every time the boat is raised or lowered, there is internal wear on the cable. Each strand of wire in the winding is moving at a slightly different speed. Abrasion of the cable strands is the result. When the strands break, they lose strength.
Assuming the cable is well cared for, how long should it last?
Experts say that to be safe- replace a galvanized cable every two years. All things being equal, the stainless cable will last longer. Up to 2X as long.
A point often overlooked – internal abrasion and rust are hidden, and there may be no visible damage. A boat lift cable like this will fail without prior warning.
When in doubt, plan on replacing the cables. Trying to squeeze another year out of a $75 cable isn’t worth the risk of dropping your boat or personal injury.
PWS handles Shoremaster cables and can provide new cables for all brands.
Nothing lasts forever – even boat lift cables.
Don’t Forget – Considering rip-rap for your shoreline? PWS is the place to contact!
Where is Pier & Waterfront Solutions?
Located at 7325 St. Hwy 57, it’s 3 miles south of Sturgeon Bay, and 1 mile past the intersection of Cty MM (heading north). Look on the right side, one mile north, at the next intersection (Idlewild Road and Hwy 57).
ARE WE OPEN?
During this time of uncertainty, Pier & Waterfront Solutions is staying “open.” We have implemented measures to ensure the safety of our employees and visitors. At the same time, we are working to maintain the trusted service that you have come to expect.
We are implementing these precautionary measures:
1. Conducting as much business as possible by email, text, or phone.
2. Site visits will continue but with limited in-person meetings. When in-person contacts are necessary, we will follow “social distancing” guidelines.
3. Our display yard is always open for you to examine at your leisure. All displays have a numbered, red tag on them. If you want more information or pricing, please reference that number.
Is there More?
4. Some employees will be working remotely, but they are always available by phone.
5. Any employee with symptoms or illness is sent home.
6. We continue to provide estimates and invoices by email to make the process paperless.
7. Crew starting times are being staggered to limit social interactions.
8. We keep the same crews together to limit cross interactions.
With these measures, we hope everyone will stay safe, and we will be back to normal operations soon.
What can you do to help us?
1. Please conduct as much business as possible via emails, messaging, and emails. This step protects everyone involved.
2. When you see our crews installing equipment, please practice “social distancing.”
Thank you for allowing us to work with you.
So – YES – ARE WE OPEN?
Please call, message, or email us with any questions.
Let’s all stay safe!
Contact:
Jerry @ (920) 493-4404 or Jerry@wisconsinpws.com – Commercial work & new/used Sales.
Dave @ (920) 905-2588 or Dave@wisconsinpws.com – Erosion control & shoreline work.
John @ (920) 493-4405 or John@wisconsinpws.com – Scheduling & Service work
May 5, 2020
Sturgeon Bay business installs Rip-Rap
Pier & Waterfront Solutions has expanded its Sturgeon Bay rip-rap business to handle the increased installation demand on Lake Michigan and the Bay of Green Bay. Installing rip-rap has prevented further destruction due to the high water levels. Pier & Waterfront Solutions has kept its excavators working through the winter to meet the demand.
PWS Co-owner, Dave Kalista, has been coordinating the work for the last two years. Dave recently reported that “As the waters continue to rise, the demand has risen with it. We recently added another excavator to handle the demand.” Dave went on to say, “With the additional excavator, we can better serve our customers in a timely fashion.”
As of Jan. 2020, local waters in Sturgeon Bay and the whole of the Door County Peninsula have risen 39,” year-to-year. 39″ exceeds records set back in 1986. Some experts predict water levels will increase by an additional 20″ by the end of summer.
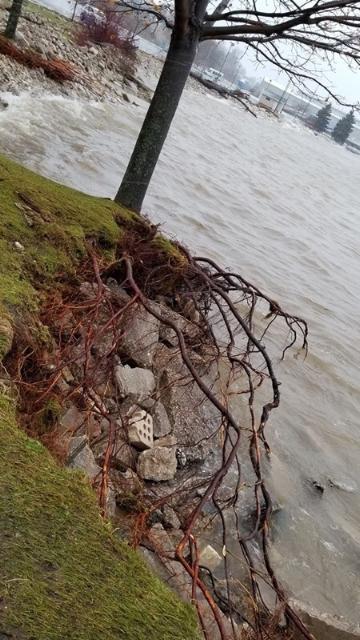
Rip-rap could prevent this.
As a result, beaches are eroding at an alarming rate. The erosion is due to record-setting water levels and intense storms. Typical damage includes eroded beaches, lawns, and uprooted trees and vegetation.
How can you protect your Property?
Experts agree – rip-rap and seawalls are the best methods to protect against erosion. Of the choices, rip-rap is the least costly by far.
Contact Dave at (920) 905-2588 for more information.
Where is Pier & Waterfront Solutions?
Located at 7325 St. Hwy 57, it’s 3 miles south of Sturgeon Bay, and 1 mile past the intersection of Cty MM (heading north). Look on the right side, one mile north, at the next intersection (Idlewild Road and Hwy 57).
ARE WE OPEN?
During this time of uncertainty, Pier & Waterfront Solutions is staying “open.” We have implemented measures to ensure the safety of our employees and visitors. At the same time, we are working to maintain the trusted service that you have come to expect.
We are implementing these precautionary measures:
1. Conducting as much business as possible by email, text, or phone.
2. Site visits will continue but with limited in-person meetings. When in-person contacts are necessary, we will follow “social distancing” guidelines.
3. Our display yard is always open for you to examine at your leisure. All displays have a numbered, red tag on them. If you want more information or pricing, please reference that number.
Is there More?
4. Some employees will be working remotely, but they are always available by phone.
5. Any employee with symptoms or illness is sent home.
6. We continue to provide estimates and invoices by email to make the process paperless.
7. Crew starting times are being staggered to limit social interactions.
8. We keep the same crews together to limit cross interactions.
With these measures, we hope everyone will stay safe, and we will be back to normal operations soon.
What can you do to help us?
1. Please conduct as much business as possible via emails, messaging, and emails. This step protects everyone involved.
2. When you see our crews installing equipment, please practice “social distancing.”
Thank you for allowing us to work with you.
So – YES – ARE WE OPEN?
Please call, message, or email us with any questions.
Let’s all stay safe!
Contact:
Jerry @ (920) 493-4404 or Jerry@wisconsinpws.com – Commercial work & new/used Sales.
Dave @ (920) 905-2588 or Dave@wisconsinpws.com – Erosion control & shoreline work.
John @ (920) 493-4405 or John@wisconsinpws.com – Scheduling & Service work